Digital Twin
Czym jest Digital Twin?
Pod nazwą Digital Twin (pol. cyfrowy bliźniak) kryje się wirtualny model. Może być on idealnym odzwierciedleniem obiektu fizycznego, procesu lub systemu. Modelem Digital Twin nazywa się połączenie fizycznego obiektu wraz z jego cyfrowym odwzorowaniem w przestrzeni wirtualnej. Całość realizowana jest za pomocą możliwości przetwarzania danych w czasie rzeczywistym i stałej aktualizacji stanu obiektów i procesów w nich zachodzących.
Jako przykład pomagający zrozumieć ideę cyfrowego bliźniaka można podać tu silnik rakietowy. Jest on wyposażony w wiele czujników, które odnoszą się do ważnych obszarów funkcjonalnych. Czujniki te dostarczają danych takich, jak na przykład emisja energii, poziom spalania czy temperaturę. Dane następnie przesyłane są do systemu przetwarzania i przesyłane do kopii cyfrowej. Dzięki nim, dany model wirtualny może zostać użyty to przeprowadzenia symulacji, badania wydajności lub generować możliwe ulepszenia. Wszystko ma na celu generowanie cennych informacji w celu usprawnienia całego obiektu czy procesów w nim zachodzących, który następnie można przenieść na model fizyczny.
Symulacje a Digital Twin
Zarówno powszechnie znane symulacje jak i Digital Twin wykorzystują cyfrowe modele do odtwarzania wszelkich rodzajów procesów. Różnica jednak w tym, że cyfrowy bliźniak już sam w sobie jest wirtualnym środowiskiem, a to oznacza, że może samodzielnie przeprowadzić dowolną liczbę potrzebnych oraz wartościowych symulacji w celu zbadania wielu zachodzących procesów. W porównaniu symulacja zazwyczaj bada określony wskazany proces. Dodatkowym aspektem na korzyść Digital Twin jest fakt, że symulacje nie korzystają z danych w czasie rzeczywistym, podczas gdy sam zaprojektowany jest z uwzględnieniem dwukierunkowego przepływu danych i informacji. Przepływ ten zaczyna się w momencie, gdy czujniki obiektu dostarczają istotnych danych do procesora systemowego. Kończy się w chwili udostępnienia informacji wygenerowanych przez procesor do obiektu źródłowego.
Za pomocą bardziej specyficznych i stale aktualizowanym danym z wielu obszarów działania obiektu oraz dodatkowej mocy obliczeniowej, która zapewniana jest przez środowisko wirtualne. Digital Twin jest w stanie badać większą ilość problemów z dużo szerszej perspektywy niż porównywana tradycyjna symulacja. Dzięki temu, ma również większy potencjał w zakresie ulepszania produktów jak i procesów.
Typy Digital Twin
Component Twins / Parts Twins
Pierwszym typem, który opiszemy jest cyfrowy bliźniak pojedynczego komponentu z całego systemu. Są to kluczowe komponenty, które mają bezpośredni wpływ na wydajność oraz funkcjonalność. Drugim zastosowaniem są natomiast podzespoły o mniejszej ważności, które w dalszym ciągu są stale narażone przez przeciążenia.
Asset Twins
Typ opisujący, w jaki sposób poszczególne komponenty całości współpracują ze sobą. W przypadku gdy Component Twins skupiają się na stabilności i trwałości konkretnych części, Asset Twins umożliwia eksplorację całego systemu. Za ich pomocą można sprawdzić, w jaki sposób poszczególne elementy współpracują ze sobą oraz poznać możliwe ulepszenia. Wszystko bez konieczności działania na realnym obiekcie. Jeden z największych benefitów takiego zastosowania? Zmniejszenie czasu między awarią a czasem naprawy przy jednoczesnym zwiększeniu wydajności.
System or Unit Twins
Następny typ łączy ze sobą pojedyncze Asset Twins i daje możliwość sprawdzenia w jaki sposób ze sobą współpracują (podobnie do Asset Twins, łączących poszczególne Component Twins). Jeszcze raz wróćmy do przykładu silnika rakietowego przytoczonego na samym początku. System Twins łączy w sobie wszystkie niezbędne zasoby do napędu, zasilania itp. Sam system można wykorzystać w przeróżnych przypadkach. Dla lepszego zrozumienia można podać tu przykład całej fabryki samolotów. W tym przypadku System or Unit Twins gromadzi wszystkie jednostki, które są niezbędne do produkcji części gotowego samolotu. Jego działanie skupia się także na poprawie współpracy pomiędzy poszczególnymi komponentami. Otrzymanym efektem jest maksymalizacja wydaności przy minimalnym czasie oraz zużyciu materiałów.
Process Twins
Ostatnim typem Digital Twins jest Process Twins. Dla ułatwienia zostańmy przy przykładzie samolotów. Process Twins reprezentuje kompletne zakłady produkcyjne dającym wgląd w współprace wszystkich poszczególnych jednostek. Ważny jest czas, a w całym cyklu może się zdarzyć, że poszczególne jednostki produkują zbyt szybko lub wolno. W pierwszym przypadku kończy się to nadmiarem elementów, co prowadzi do niepożądanych kosztów magazynowych. Drugi przypadek również wiąże za sobą niepożądane skutki, a więc w celu uniknięcia ich przedsiębiorstwa korzystają z technologii Digital Twin. Dzięki niemu można zobaczyć całą złożoność jaką cyfrowy bliźniak nadzoruje, aby wszystkie komponenty spełniały swoje zadania. W efekcie otrzymujemy proces jak najbardziej funkcjonalny i efektywny.
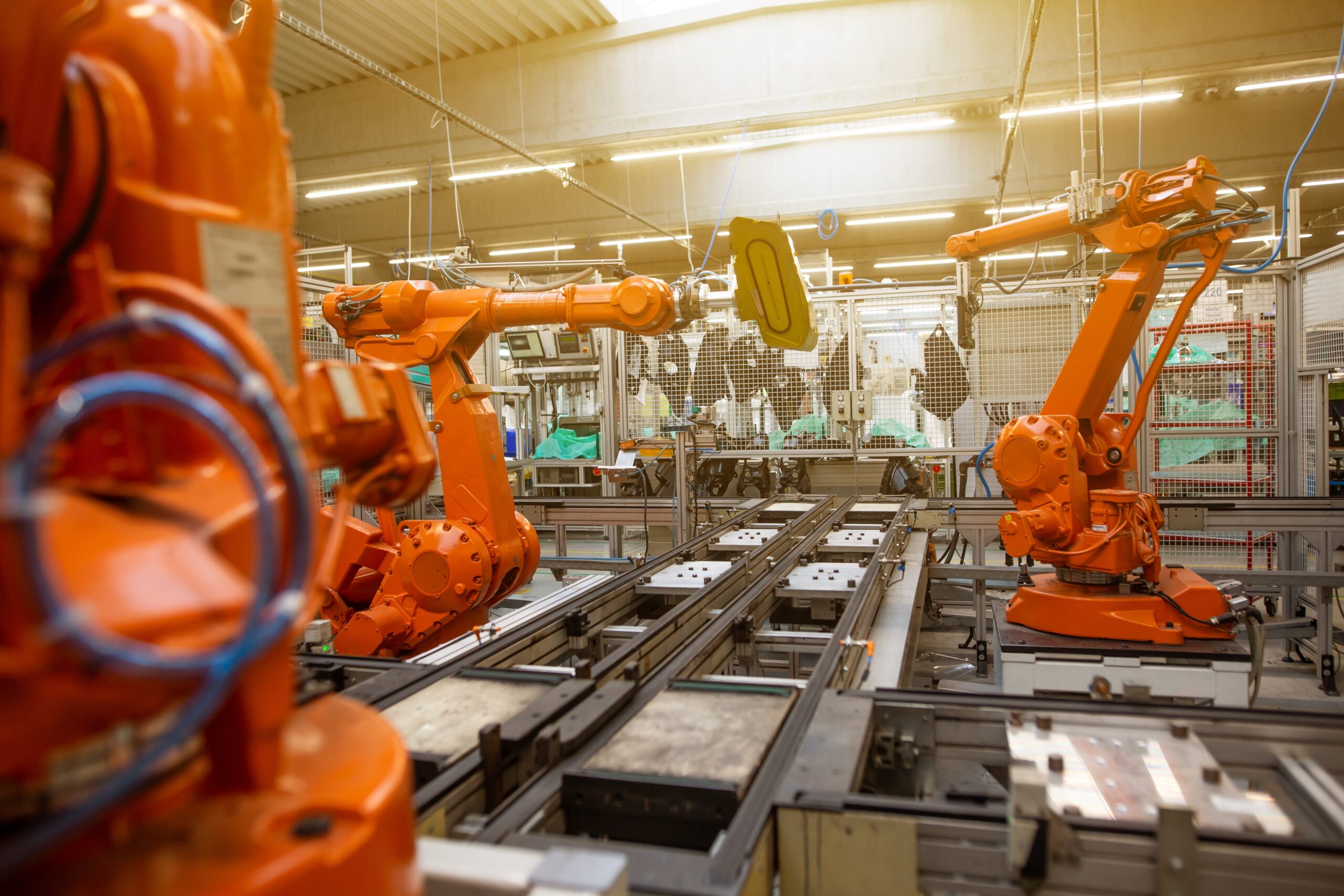
Zalety i korzyści Digital Twin
Badania i rozwój
Wykorzystanie cyfrowych bliźniaków pozwala na przeprowadzenie bardziej efektywnych badań i projektów produktów, generując ogromną ilość danych na temat prawdopodobnych wyników. Informacje te mogą dostarczyć wartościowych insight’ów, które pomogą firmom dokonać niezbędnych udoskonaleń produktu jeszcze przed rozpoczęciem procesu produkcji.
Większa wydajność
Nawet po wprowadzeniu nowego produktu do produkcji, Digital Twin może pokazać „lustrzany” podgląd i monitorować systemy produkcyjne w celu osiągania i utrzymywania maksymalnej wydajności w całym procesie.
Koniec cyklu życia produktu
Cyfrowy bliźniak pomaga producentom decydować, co zrobić z produktami, których cykl życia dobiega końca i muszą zostać poddane przetworzeniu. Digital Twin jest w stanie określić, które materiały są wartościowe i mogą zostać zebrane.
Prognoza rynkowa i rodzaje zastosowań
Według danych z MarketsandMarkets, wartość rynkowa Digital Twin w 2022 roku kształtuje się na kwotę 6.9 miliarda USD. Zgodnie z przewidywaniami może ona wzrosnąć aż do 73,5 miliarda USD w ciągu najbliższych 5 lat. Niewątpliwie wpływ ma na to przemysł 4.0 oraz stosowanie danej technologii w wielu przypadkach. Jako przykład można podać tu moduły do wytwarzania energii takie jak silniki czy turbiny. Struktury wraz z ich systemami takie jak budynki czy na przykład platformy wiertnicze chociażby poprzez systemy HVAC (ogrzewanie, klimatyzacja i wentylacja). Wspomniane już procesy produkcyjne, przemysł motoryzacyjny czy nawet planowanie miast i usługi zdrowotne. W ostatnim przypadku pacjenci mogą być profilowani za pomocą Digital Twin do śledzenia wskaźników zdrowotnych i generowanie ważnych informacji pozwalających na ratowanie życia.
Jak widać po przytoczonych przykładach, projektów które odnoszą szczególne korzyści za pomocą cyfrowego bliźniaka jest wiele. Warto jednak mieć na uwadze, że zastosowanie Digital Twin nie jest słuszne dla każdego przypadku. Nie każdy obiekt jest wystarczająco skomplikowany, aby wymagał intensywnego i regularnego przepływu danych przez niezbędne czujniki. W efekcie może być to nieopłacalne finansowo, z uwagi na replikę danego procesu lub obiektu 1:1, która również generuje koszt.
Chcesz dowiedzieć się więcej? Umów się na bezpłatną konsultację!